Ремонт двигателей
Качество, прежде всего.
В моей мастерской огромное значение уделяется качественному ремонту двигателей. Это кропотливый труд, за которым стоит, надежная и долгая работа отремонтированного двигателя.
Как повелось издавна лучше один раз долго, но качественно. Быстрота, «как правило, не качественная работа», рано или поздно напомнит о себе в самое не подходящее время. А то есть когда ты занят другой срочной работой. А клиент, как правило, ждать не хочет.
Качество ремонта заключается не только в качественной работе по закручиванию гаек и болтов. Но и в контроле деталей, которые будут установлены на двигатель.
Нередки случаи, когда токарь-расточник, после будуна или заморочки проточил шейку коленвала в недопустимом размере, что будет, если не проверить? Да в одном случае скоро застучит, если не сразу, а во втором провернет вкладыш, когда нагреется. И тогда опять разборка с походом на авторынок за новым шатуном и в зависимости от конструкции двигателя за комплектом поршней.
Так как поршень может поломаться при выпрессовке поршневого пальца. А что коленвал! так тот опять попадет на стол к расточнику….
Все расходы, по всей видимости, лягут на мастера.
Он же собирал!
Вот и приходится знать все размеры и допуски, в сопряжениях деталей на зубок.
Зато какую радость испытываешь после первого запуска, ожившего мотора.
Когда в нем не слышно стуков, а довольный клиент наслаждается безукоризненной работой сердца его автомобиля.
Ремонт двигателя
Лакмусовой бумагой, для клиента позволяющей отличить моториста-профессионала от дилетанта, является отношение к контрольно измерительным приборам при сборке узла. И дело не только в том чтобы измерять, необходимо понимать смысл этих измерений, а для этого моторист должен знать технологию ремонтных операций, не входящих непосредственно в процесс сборки двигателя, например, как шлифуют коленчатый вал или растачивают блок цилиндров.
Зачем, спросите? Ведь расточник по размеру поршней сам может определить
размер цилиндра, а после обработки проконтролировать результат.
Действительно может, но только ответственность за сборку несет моторист.
Так что делайте выводы, стоит ли тратить драгоценное время на контрольные замеры.
Или ими можно пренебречь.
И так за дело.
Двигатель снят с автомобиля, помыт, начинается разборка.
Устанавливаем двигатель или вывешиваем на специальном приспособлении. Снимаем навесное оборудование и производим осмотр его.
Снимем ремень или цепь привода ГРМ. Откручиваем распредвалы, осматриваем на повреждения кулачки, и шейки вала. Для чего вооружаемся так называемым микрометром для измерения шеек вала. Сопоставляем измеренные значения с допусками на износ для каждого двигателя индивидуально. СМ. ремонтные размеры завода изготовителя. После чего измеряется износ в подшипниках скольжения распредвала и
делаются соответствующие выводы. А также осевое смещение распредвала.
Откручивается головка блока цилиндров, очищается привалочная плоскость головки блока и лекальной линейкой проверяется деформация ГБЦ. Если величина превышает 0.1 мм. головку следует отфрезеровать.
Измеряем их длину, если длина не известна, то самые длинные растянулись, заменяем новыми, иначе при сборке они не смогут затянуть ГБЦ.
Иначе после сборки двигателя в период обкатки, возможно, произойдет разрушение прокладки, и охлаждающая жидкость может попасть в масло, образованием эмульсии порой такой густой как «Литол». Что произойдет, если за рулем находится «Чайник» или «Нерадивый» хозяин представить трудно.
Но не стоит забегать в период.
Откручиваем впускной и выпускной коллектора ГБЦ к блоку цилиндров.
Очищаем камеры сгорания круглой щеткой установленной в дрель, осматриваем головку, на предмет трещин между седлами клапанов и в рубашку охлаждения. Рассухариваем клапана и извлекаем, установив их в специальное приспособление для удержания в определенном порядке, для последующей установки в привычные места. Осматриваем стержни клапанов и если на них есть масло, можно сделать вывод что из-за устаревших сальников клапанов происходил, угар масла. Измеряем, диаметр клапана микрометром, и его длину при необходимости меняем. Очищаем тарелку клапана от нагара можно, зажать клапан в дрель и зачистить наждачной бумагой до блеска. Если на рабочей фаске имеются трещины и глубокие точки, заменить новым. Если новый клапан болтается в направляющей втулке необходимо поменять и ее. Но случается, так что после замены втулки и райберовки седла клапана для регулировочной шайбы не остается места. Вот тут и стоит задуматься над целесообразностью ремонта ГБЦ. Возможно, ли будет отрегулировать тепловые зазоры, после сборки узла. Далее, проверяем состояние натяжителя цепи, если он исчерпал, свой запас, то необходимо заменить цепь, не рекомендую надевать на натяжитель всякие наставки, цепь натянется, а вот газораспределение останется установленным не правильно. Неточность допускается всего +/- 2 гр. Это по отношению к двум оборотам коленчатого вала, то есть 720 гр. Только от растянутой цепи можно не досчитаться 5 лошадиных сил. Необходимо также проверить состояние звездочек, их зубьев, успокоителя и натяжителя.
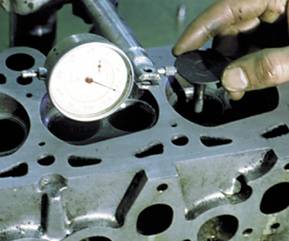
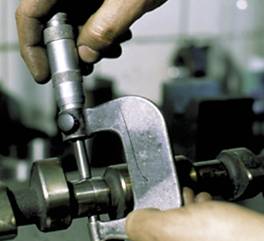
Приступаем к разборке блока цилиндров
Откручиваем корзину сцепления, если на ней есть потертости от заклепок диска сцепления и присутствуют микро трещины, заменяем, корзину вместе с диском.
Проверяем диск, если присутствуют неровности можно диск проточить на токарном станке. Хуже не станет, зато сэкономим кучку денег и пустим их на другие запчасти.
Снимаем крышку цепи и саму цепь, откручиваем гайки шатунов, снимаем крышку шатуна и на коленвал поперек укладываем щуп толщиной 0.1 мм длиной по ширине вкладыша, (метод конечно дедовский, но безотказный) закручиваем гайки необходимым моментом.
Поворачиваем коленвал руками, поворачивается с трудом, необходимо поменять вкладыши и сделать повторный замер.
Если он прокручивается, значит, шатунные шейки коленвала надо ремонтировать.
Также поступаем с коренными подшипниками коленвала, но щуп используем 0.15мм.
Метод простой, но достаточно эффективный, когда нет микрометра.
Снимаем поршня, заведомо открутив гайки шатунов, осматриваем поршня. Первый этап проверки заключается в измерении зазора между кольцом и поршнем, который не должен превышать 0.1 мм. Для чего необходимо взять щуп и попытаться просунуть его
в щель. Если с трех сторон щуп не проходит в сопрягаемых участках, то значит поршень, исправен. Как правило, больше всего подвержены износу верхние компрессионные канавки. Можно поставить новое кольцо в канавку и проверить зазор если он не превышает допустимое значение, то поршня можно использовать дальше.
Как правило, это наиболее частая неисправность поршней, за ней стоит разрушение перегородок поршня, а износ между поршнем и цилиндром наблюдается еще реже.
Если износ в канавке не большой, то демонтируем кольца с поршней, и вставляем их в цилиндр, проталкивая их поршнем на глубину примерно 20 мм. Измеряем щупом зазор в стыке кольца, который не должен превышать 0.15 мм. Во всех кольцах.
Наиболее часто изнашиваются чугунные маслосъемные кольца, стальные диски подвержены меньшему износу. И в окончание, шатуном в низ помещаем поршень, в двигатель, поршень должен, находится в ВМТ, берем щуп и замеряем зазор между сопрягаемыми деталями. Предельно допустимый зазор составляет 0.15 мм.
Также необходимо проверить осевое смещение коленвала, которое, не должно превышать
0.25 мм. На этом Дефектовка заканчивается.
Приступаем к мойке снятых деталей двигателя, поскольку процесс мойки занимает очень много времени и сил, подробно останавливаться на этом не будем.
Пока блок цилиндров и коленчатый вал растачивается, мы отправляемся за запчастями на рынок или магазин, большого значения не имеет, главное купить то, что нужно из большого количества подделки и брака.
Ну, вот все этапы пройдены; блок цилиндров после расточки отмыт и выкрашен,
коленчатый вал продут воздухом, все готово для сборки.
Устанавливаем коренные вкладыши, в блок цилиндров, соблюдая чистоту и аккуратность, смазываем их моторным маслом. Берем измерительный прибор и проверяем работу расточника измерив, все шейки коленвала. Ложем коленвал на вкладыши. Оставшуюся часть вкладышей укладываем в бугеля и устанавливаем их на место. Предварительно затягиваем болты бугелей, покручивая колено, убеждаемся, не закусывает ли. Мы для полной уверенности в работе проверяем щупом зазоры, но теперь уже другими, а то вдруг вкладыши брак. Берем щуп 0.03 и тем же способом проверяем зазор, вал должен без препятствий проворачиваться, иначе нагреется и провернет вкладыш. Потом проверяем щупом 0.06 мм, должно легко прикусывать, это оптимальный зазор, 0.03 сотки масляная пленка и оставшаяся часть тепловое расширение. После этого не плохо было бы проверить на максимальный зазор, но надо постепенно затягивать болты, чтобы не повредить поверхность сопрягаемых деталей и если деталь перестала проворачиваться стоит прекратить дальнейшую затяжку.
У меня бывало, так что после проточки коленвала для ЗМЗ 406 я не мог собрать двигатель клинили, как шатунные, так и коренные вкладыши. Причем они соответствовали указанному размеру самим токарем. Поскольку был выходной у токаря, на месте его не оказалось, то хозяину пришлось купить новое колено, после чего все стало нормально.
А самый первый казус это двигатель 2103, который я собрал, не проверяя зазоров. Что оказалось в последствии, после удачного и легкого запуска, минут через 30 он начал издавать писк. В недоумении и посовещавшись с товарищами, я полез в кривошипно-шатунный механизм. Благо это была не «Нива». Причина простая мал зазор между вкладышем и коленвалом. При нагревании деталь расширялась и вытесняла масло, крутясь на сухую, тут и до беды не далеко.
А проверь я при сборке, сопрягаемые детали не пришлось бы тратить время на переделки, с большими трудозатратами.
Собираем дальше, берем поршня и измеряем зазор между поршнем и цилиндром.
Разные двигателя разные зазоры, кто-то рекомендует 0.035, а кто и 0.06 мм.
Я не делаю маленьких зазоров в этих деталях, так как поршень чаще изнашивается не в этом месте. А вреда при маленьком зазоре много:
1. При нагреве двигателя поршень начинает драть цилиндр, сильно изменяя в период обкатки и не только его диаметр, да и сам безнадежно стираясь.
2. А поскольку цилиндры становятся неровные, появляется угар масла!!!!
Кольца не могут снять остатки масла в подранных участках. Ремонт не удался…
3. Этому присущ тяжелый или невозможный запуск двигателя сразу после его остановки.
Надо ждать, когда остынет.
Приступаем к ремонту головки блока.
Технологической базой для обработки седел клапанов служат направляющие втулки клапанов.
При измерении отверстия зазор превышает допустимый размер, предварительно высверливаем ее до толщины стенки 1-2 мм для меньшего натяга и потом выбиваем окончательно. Общее правило гласит для любых двигателей, нельзя запрессовывать детали без предварительных измерений фактического натяга. Запчасти для отечественных АВТО просто бывают бракованные. В идеальном случае перед запрессовкой надо обеспечить разность температур головку нагреть, а втулку охладить. Запрессовку выполняем быстро 2-3 ударами молотка.
Некоторые мотористы запрессовывают втулки «вхолодную» это плохо алюминиевый сплав деформируется и реальный натяг уменьшается. После остывания головки втулки калибруются развертками. Как на рисунке. Обработав отверстие надо обязательно проверить зазор. Для впускных клапанов он должен быть в пределах 0.02-0.04 для впускных 0.03-0.04мм. Иначе клапана во втулках могут заклинить.
После этого необходимо обеспечить соосность между втулкой и седлом клапана и создание определенного профиля седла рекомендуемого заводом изготовителем. Для обработки применяем ручной инструмент угловые фрезы при вершине 30, 45 и 60 гр. Много стараний по соблюдению соосности необходимо применить, любой даже маленький перекос не приемлем. Иначе седло будет долго притираться клапаном, на котором появится преждевременный износ. При работе ДВС произойдет разрушение клапана, поскольку он не будет прижиматься к седлу и остывать равномерно. Во втулке клапана быстро образуется недопустимо большой зазор. Многие мотористы говорят так «притрется», в чем сильно не правы. Представьте, все после ремонта быстро притирается. Зачем тогда нужны инструменты? Втыкаем, собираем, прикручиваем и все! Ведь из-за неквалифицированного ремонта двигателя ломаются снова, и снова и притирка не помогает…
После совмещения втулок и седел притираем абразивной пастой, но не более 1 мин. Если притирка длится дольше, на седле серый поясок разрывается, значит все плохо. Седло перекошено не прихлопается…
Закончили с притиркой, детали очищаем промывкой, смазываем моторным маслом и собираем.
Предварительно регулируем клапана и если все нормально. Прикручиваем навесное оборудование.
Прокладку ГБЦ размещаем на сухую поверхность блока, что бы не повредить прокладку кладем головку. Предварительно смазанные болты моторным маслом прикручиваем в порядке указанным заводом изготовителем, динамометрическим ключом к блоку.
Сборку можно считать законченной, остается установить двигатель на автомобиль.